Over the last few decades, we’ve seen 100s of reel to reel tape decks through our doors, from early 1950s mono tube machines, to mid-1980s studio multitrack units. While there are many unique problems with reel to reels that we are still discovering almost every week, there are a bunch of common failures that occur to every unit, and then there are specific issues related to each brand. While we can’t touch on all of them, we can cover some.
A reel to reel recorder has a mechanical transport, be it completely mechanical, or in conjunction with solenoids and some sort of controller or microprocessor board, and then the record and playback circuits are electronic, so there are two types of failures that can occur in these machines. More often than not, there are issues in both the transport and the electronics, resulting in time consuming repairs, and as with any repair industry, labour is the most expensive portion of the job, so it’s not uncommon for a repair to easily outweigh the value of an older or lower end recorder. While a complete novice shouldn’t dive headfirst into a high end expensive reel to reel, there’s usually no harm done in taking off the cover of a recorder, especially if you got it for free. Caution is to be exercised, as we have seen many machines turn from simple problems into write-offs because someone got into the unit and started replacing parts at random, or used the wrong chemical to attempt to clean or lubricate the machine. Let’s start with some very basic problems:
Electronics/Audio circuits
The most common problem with any reel to reel that hasn’t been serviced in years is dirty switches and controls. By that we mean the contacts in a switch or a rotary/slide control have become intermittent due to contact oxidation. This can result in a dead audio channel, or cause the cutting in and out of sound as a switch is wiggled, or a volume control is turned. This is almost always solved via the use of contact cleaner applied to the contacts or controls. While we could write pages just on how to clean controls, here’s some basics:
- The best contact cleaner we have found is by a company called Caig, who make many products, but we generally use the DeOxIt brand of contact cleaner. www.caig.com Caig DeOxIt is generally more expensive than the $10 bottles of spray cleaner found at Radio Shack, but a light application will last years, whereas cheaper contact cleaner may need to be reapplied within a year or two.
- Apply contact cleaner SPARINGLY! It says that right on the bottle of DeOxIt in fine print, but who reads that, right? Use the plastic nozzle to aim into the control or switch, and a very short burst should be plenty to clean the control.
- Immediately after applying the control cleaner, run the switch through all positions several times, or rotate the level control through the full range several times. If you aimed the plastic nozzle properly, the control should now be free of noise.
- Most switches and controls have some sort of opening so that contact cleaner can be applied to the noisy control, but some higher end controls may be hermetically sealed. In some cases we’ve been able to use a tiny drill to put a hole into the sealed control, but you also risk damaging the control itself. Proceed at your own risk!
- DO NOT use WD40 or a non silicone based cleaner, as you can damage the control permanently.
- Some controls may be physically broken internally, and no amount of control cleaning will fix a damaged volume control.
- Any male/female connector within a tape recorder can also use a shot of control cleaner. Some makes of tape decks use internal modules that plug into a motherboard, and those contacts can also use a light shot of control cleaner for a better connection.
- DO NOT adjust internal controls and small adjustable controls (trim pots) at random! Almost all of these control settings are critical to the proper operation of the tape deck, and random adjustment of the controls can kill a tape deck.
Burned out Dial Lights
Since most reel to reels were made before LEDs became affordable, most decks used incandescent lights to illuminate function buttons and VU meters. There are a large variety of lights used in the various decks. If you feel comfortable replacing small bulbs in cramped quarters, download the service manual which will usually tell you the voltage rating of the bulbs. Most run at 6, 8 or 12 volts, but there are also some decks that use 24 volt bulbs. Some bulbs use sockets, but many are soldered in place.
Tape Heads
While there is a separate section here on worn tape heads, it is a common misconception that TAPE HEADS NEED REALIGNMENT! What most people don’t know, including some rookie techs, is that tape deck head alignment screws are sealed at the factory, and not even heavy scrubbing of the tape heads will knock them out of alignment. A worn tape head cannot be brought back to life with tape head alignment. If you do not have the knowledge or calibration tapes, DO NOT ATTEMPT TO ALIGN THE TAPE HEADS. More than once, we’ve worked on a deck that appeared to still have the seals intact on the tape head screws, only to find that someone had indeed tried to align the tape path without the proper knowledge or test equipment, and made a simple repair job much worse.
Ditto for all of the small adjustment controls on the PC boards that are for various levels, biasing and equalization of the tape heads. Even an incorrect 1/8 turn of one of those controls can throw one or both channels way out of whack.
Mechanical Issues
Very common with reel to reels are some sort of mechanical issue. Let’s look at a few:
Stretched/Broken Belts
Many reel to reels used some form of belt to transfer power from one or more motors to the tape transport. Over time, the belts can stretch, break, or worst case, turn to goo, which can and will send remnants of liquefied rubber belt all over the inside of the transport. Get a tiny bit of liquid rubber on your fingers, and you’ll be wearing it for 2-3 days.
Accessing the belt(s) in a reel to reel will require taking off the back or front cover(s) of the tape deck, and then usually a portion of the mechanism needs to be removed to access some part of the belt path within the deck. Again, proceed only if you are comfortable here. Small springs can shoot across the room and be lost forever, ditto for C clips and other portions of the transport.
Replacement belts can usually be found on ebay, or from a list of suppliers in our referral section. Don’t use a regular rubber band! You’ll get speed variations at best, and you’ll damage internal bearings at worst due to the wrong tension. Some decks are all direct drive motors, with only the tape counter needing a belt… sometimes. Check the service manual to see if your make and model has a belt or two or three in it.
Weak or worn rubber Components
Every reel to reel has a degree of rubber components in it, if nothing else, the pinch roller that connects to the capstan shaft to drive the tape is made of rubber. Single motor decks will have a number of rubber idler wheels for the fast forward, rewind and play functions use a series of these wheels to transfer the motor motion to the reels and to the capstan shaft. The rubber used on these wheels can harden, become dirty or slick, and they will start to slip, giving uneven speeds and slow or nonexistent fast forward or rewind, or both.
There is a product available from electronic suppliers that comes under several names, including Rubber Renue. This liquid is applied to the rubber idler wheels and removes the top coating of rubber to expose fresh, pliable rubber below the surface. Depending on the amount of wear or hardening of the rubber idler wheel will depend if the Rubber Renue will bring the wheel back to life. We’ve seen some cases where the chemical works perfectly. Other idlers will work for a time, then harden up again, and others have hardened to the point of no return. Again, ebay is a source for possible replacements, or you may n4eed to find an identical model as a donor parts unit. In more than one extreme case of a hardened idler wheel, we were able to use a small Dremel type of tool with an abrasive disc on it to take off a layer of hardened rubber. Only attempt this if all other methods of reconditioning the rubber idler have failed, and you’re about to write the deck or the idler wheel off.
Seized Bearings
Many tape recorders use simple sleeve bearings for portions of the mechanism, as they were cheap to manufacture, and were usually pretty reliable. The problem is, 40 years after the decks were made, some formulas of sleeve bearings will seize up, not due to the bearing itself, but due to the white lithium grease that was originally used to lubricate the sleeve bearing. It hardens up, and even a tiny amount will bring a mechanism to a screeching halt. Below is the sleeve bearing of a Teac RTR machine, which I pull apart and lubricate even if they are working fine, they fail that often.
These bearings can always be unseized, but usually it involves applying heat to the bearing, then dismantling a section of the mechanism to clean the bearing out completely of old grease, and then applying a thin layer of new grease. Not for the faint of heart!
Bad Motors
Motors are generally reliable in reel to reels, although the older (pre 1973 or so) decks usually have only one motor to drive the whole tape transport. It’s not uncommon for these older motors to develop speed or torque issues over time. While you can sometimes find used replacement motors on ebay from decks that have been parted out, there’s no saying how long another 40 year old used motor will last. Many motors also use what’s called motor start capacitors, which can fail, giving the impression that the motor is bad. Detailed troubleshooting is beyond the scope of this website, so if you have a bit of electrical background, you probably already know what we’re talking about. Again, lethal voltages can and will be present under the cover of a tape deck, so proceed at your own risk.
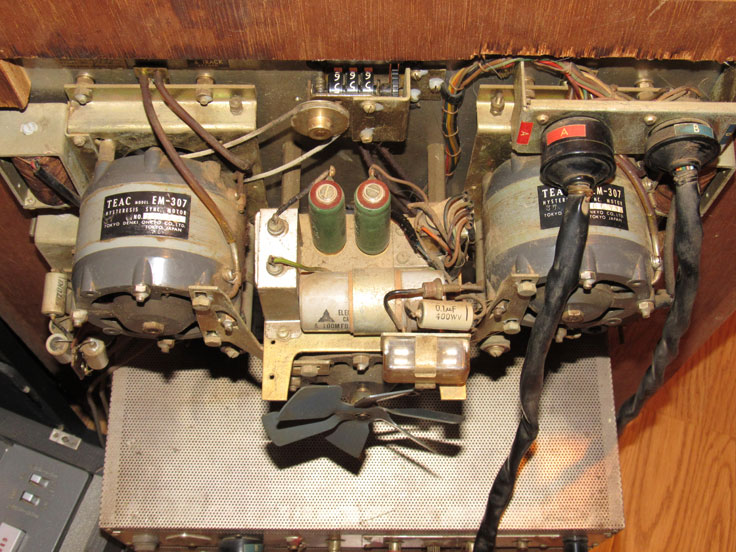
Common faults specific to brands
While this list is far from complete, here’s a list of common issues that we’ve found plague various brands of tape decks. We’ve also listed some strengths
Akai
- Dirty switches and controls, specifically the tape monitor switch
- Bad/worn/cracked rubber idler wheels (pre 1973 models)
- Worn main belts/tape counter belts
- Bad 2SC458 preamplifier transistors- multiple later models, approx 1978 and newer
- Bad LD3141 preamplifier chips –any model that uses this chip
- The GX series used glass heads which never wear out, but can fail otherwise (rarely)
- Later transports were direct drive, and simple and reliable as a result
- Earlier 4000 series dual lever transports were also very durable for the most part
- Some 4000 transports had aluminum cam issues due to bad casting. Used replacement cams are very hard to find, although overall failure is rare.
Dokorder
These decks were made to compete with Teac, Akai and Sony, but weren’t constructed very well, so we’ve seen lots of problems with the few Dokorders we’ve had in here. Bad switches, noisy controls, mechanism issues, etc. Not hard to work on specifically, but parts are hard to find as not many Dokorders were sold.
European Models (Grundig, Telefunken, Philips, Tandberg, etc)
- Many more Japanese tape decks were sold in North America compared to European models, so parts, even on the used market tend to be difficult to find.
- European decks suffer from similar problems to that of Japanese units
- The sound quality overall was similar of European decks to that of Japanese
- High end Tandberg machines were on par with Revox for the most part, but parts are much harder to find than for Revox, and some Tandberg models used custom chips which are no longer available.
Fostex
- Marketed exclusively to the home and pro market.
- The ¼” 8 track machines were somewhat weak in FF and REW due to the inexpensive transport design.
- Certain models suffered from LED VU meter burnout, which are no longer available
- The ¼” 8 track models were not high end machines, but offered great value for the money, which is why thousands were sold into the home studio market.
- The 16 and 24 track machines suffered from leaking capacitors, which leaked electrolyte onto the PC boards, causing circuit trace problems, and in many cases, causing the machine to be a write-off.
- In good working shape, the 2, 4 and 8 track models can still be great for a home studio application.
Otari
- Semi pro/pro machines, very solidly built. Most popular at radio and TV stations worldwide
- As a result of widespread commercial use, many machines are cosmetically fair to poor, but will most likely still work fine
- Heads and brakes can be worn out due to excessive or heavy use
- Dirty controls and switches
Pioneer
- Early (pre 1973) machines are to be avoided, as they have numerous problems
- Later (post 1973 RT series and the 707/909 models are excellent performers
- Stretched counter belts
- Noisy controls and switches
- Stretched or gooey main belts (very common)
- If a gooey belt wraps itself around the main motor shaft, the motor can burn out, which can be expensive ($150-200 USD just for a used motor)
- Worns heads due to heavy use
- Bad function switch contacts on some models (play, FF, REW)
Studer/Revox
- Generally very solid, well built machines
- The A77 was the first popular machine from Revox, but they are showing the signs of age
- The B77 is typically 5-10 years newer than the A77, and tends to be more reliable.
- Internal trimmer potentiometers are known to go intermittent often
- Revox used a brand of capacitor called Frako, which are known to short out
- To fully restore a Revox deck, it should have all Frako capacitors replaced, which is a time consuming and expensive proposition, but worth it if the rest of the deck is in good shape.
- B77 and PR99 models have the toggle switches as a weak point, and they can snap. They are expensive on eBay ($80 USD each or so as a result)
- The Studer machines were aimed at the pro market, and share similar characteristics to the Revox machines as they come from the same factory.
- Some versions of pinch rollers go gooey or can liquefy, occasionally resulting in motherboard and faceplate damage.
- Some machines suffer from VU meter failure due to sticking or defective meter movements.
Sansui
Not many Sansui reel to reel decks were sold compared to other Japanese brands, and they share similar strengths and weak points to Teac
Sony
- Bad/cracked/worn rubber idler wheels (all models)
- Stretched belts
- Seized sleeve bearings (almost all models, and many use multiple sleeve bearings)
- Bad motors (single motor decks)
- Bad motor start capacitors (single motor decks)
- Dirty switches and controls
- Worn capstan bearings/seized bearings due to the lithium grease
Teac/Tascam
- Stretched/gooey belts (very common)
- Gooey pinch rollers
- Seized pinch roller and other sleeve bearings
- Dirty switches and controls
- Worn heads due to the deck being very reliable overall, so they wear out due to heavy use
- Cracked PC boards at head block (Teac 3340 only)
- The reel table locks can break if the tape spindles are handled roughly. Fortunately there are lots of reel tables on eBay for relatively cheap.
- Tascam was the pro division of Teac, and pro and home studios were targeted with the Tascam line. Generally shares the same strengths and weaknesses as the Teac models.
Technics
- The 1500/1700/1800 series were very solid decks, at the high end of consumer machines
- The plastic spindles can break if handled roughly, but they are not available separately, so the whole motor has to be replaced if a spindle breaks. Very expensive, relatively speaking
- Very solid machines otherwise, other than typical noisy controls and switches
- Excellent sounding, reliable machines overall, but expensive on the used market
Vacuum Tube Tape Decks
- Generally this means the decks are pre-1968 or so, and while pro/studio tube reel to reel decks were manufactured, the good working ones are hard to find… and exceptionally expensive if they are in perfect working condition.
- Most consumer tube machines will need a lot of work, so unless you’re mechanically and electrically inclined, they are not good candidates to be reliable machines for home use.
- There is some demand for the tube preamplifier stages, as guitar players and studio techs will use them to get that ‘tube’ sound for recording purposes.